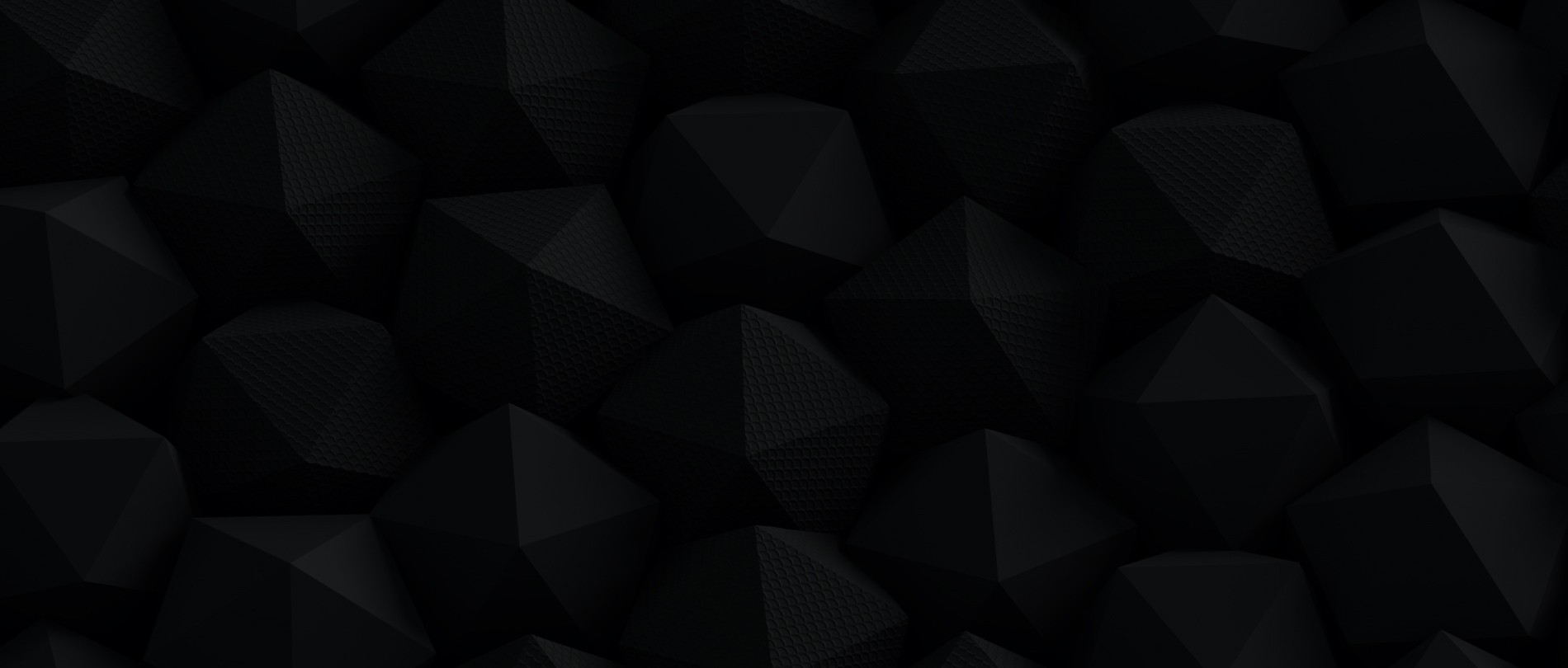
Our Journey
We dove into the research process to empathize with riggers, discover the true problems plaguing parachute packing, and help make the process better.
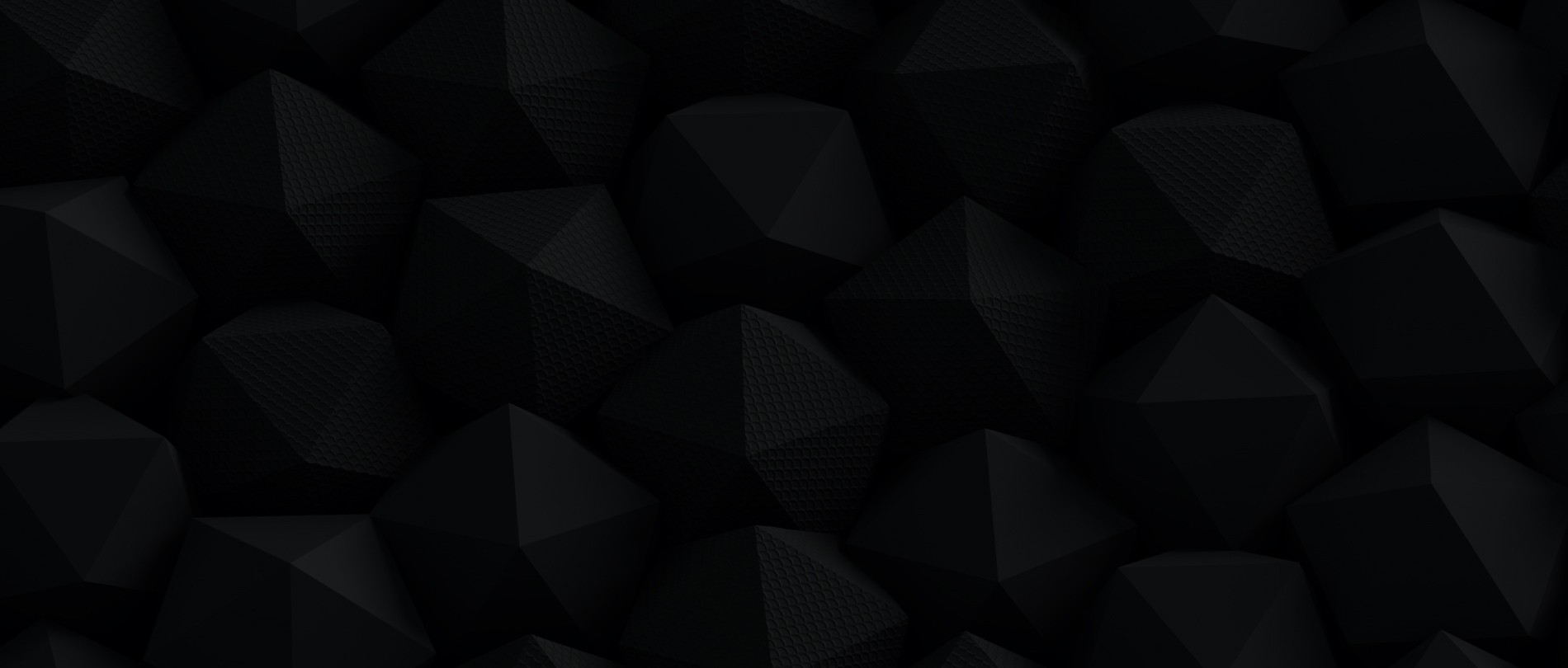
Our Journey
We dove into the research process to empathize with riggers, discover the true problems plaguing parachute packing, and help make the process better.
EMPATHIZE
Understanding our User & the Problem
The Problem
Our initial problem statement was broad, and we did not have a strong understanding of ADFSD, the parachute packing process, or parachutes in general. We had to dive into research to understand everything.
ADFSD is a US Army quartermaster school operating out of Fort Gregg-Adams in Virginia. It trains personnel for important jobs such as packing parachutes. Let's meet the users we have to empathize with in our problem space:

Riggers
Our main users—their job is to pack 15 parachutes a day.

Inspectors
Expert packers that have moved up in rank and now inspect rigger's packs during the packing process
The parachute packing process has many steps and 8 inspections total. While it is very intricate, it can be broken down into 5 main tasks:
Laying Parachute Out
Parachutes are long and slippery—this can take a while
Flaking
Folding each section of the parachute, called panels, symmetrically
Packing parachute into bag
A deployment sleeve is added over the parachute, and it is S-folded into the deployment bag
Stowing
Parachute lines need to be threaded through loops on the outside of the pack
Securing bag
Various flaps and openings need to be secured, lines need to be stored, and pins need to be checked
Here are the steps in action:
Parachute packing is slow and painstaking work—one error could lead to someone losing their life. We have been tasked with improving this process, while maintaining a low rate of errors, so that ADFSD can produce parachutes more efficiently.
Secondary Research
When we started our research, we knew very little about parachute packing. We had to do a deep dive into ADFSD, the US Army, parachutes, parachute packing itself, and the many subdomains within these categories. Once we had more general knowledge on our problem space, we decided that analogous domain research would be helpful.
This process involves looking at similar fields to your problem and seeing how that problem is solved. Parachute packing involves folding large swaths of fabric, so we researched origami, textile manufacturing, and sail making. The packing process also involves compacting something large—the parachute—into something small—the deployment bag. For this, we looked at how airbags are packed and installed in cars, or how spacecraft deployable objects are made. We were also curious if there were processes that were already automated for folding or packing large, complex pieces of material, so we researched automated manufacturing for tent and sleeping bags. While we gained valuable insights from the analogous domain research, it made us realize that there is no automated process that closely matches parachute packing. We would have to see the process for ourselves to gain a better understanding of it.

Primary Research
Next, we drove down to Fort Gregg-Adams to perform a contextual inquiry. This is a great way to empathize with the user you are designing for—by going into their environment and watching them in action.
We spent 2 days at the Fort, including touring the base and ADFSD facility, observing the riggers working, and conducting semi-structured interviews.
We used the AEIOU method, looking at Activities, Environment, Interactions, Objects, and the User. This process can involve asking questions, taking notes, and silently observing how the user does their task and how they interact with their environment.
Our research produced a wealth of findings that we still had to make sense of.

EMPATHIZE
Understanding our User & the Problem
The Problem
Our initial problem statement was broad, and we did not have a strong understanding of ADFSD, the parachute packing process, or parachutes in general. We had to dive into research to understand everything.
ADFSD is a US Army quartermaster school operating out of Fort Gregg-Adams in Virginia. It trains personnel for important jobs such as packing parachutes. Let's meet the users we have to empathize with in our problem space:

Riggers
Our main users—their job is to pack 15 parachutes a day.

Inspectors
Expert packers that have moved up in rank and now inspect rigger's packs during the packing process
The parachute packing process has many steps and 8 inspections total. While it is very intricate, it can be broken down into 5 main tasks:
Laying Parachute Out
Parachutes are long and slippery—this can take a while
Flaking
Folding each section of the parachute, called panels, symmetrically
Packing parachute into bag
A deployment sleeve is added over the parachute, and it is S-folded into the deployment bag
Stowing
Parachute lines need to be threaded through loops on the outside of the pack
Securing bag
Various flaps and openings need to be secured, lines need to be stored, and pins need to be checked
Here are the steps in action:
Parachute packing is slow and painstaking work—one error could lead to someone losing their life. We have been tasked with improving this process, while maintaining a low rate of errors, so that ADFSD can produce parachutes more efficiently.
Secondary Research
When we started our research, we knew very little about parachute packing. We had to do a deep dive into ADFSD, the US Army, parachutes, parachute packing itself, and the many subdomains within these categories. Once we had more general knowledge on our problem space, we decided that analogous domain research would be helpful.
This process involves looking at similar fields to your problem and seeing how that problem is solved. Parachute packing involves folding large swaths of fabric, so we researched origami, textile manufacturing, and sail making. The packing process also involves compacting something large—the parachute—into something small—the deployment bag. For this, we looked at how airbags are packed and installed in cars, or how spacecraft deployable objects are made. We were also curious if there were processes that were already automated for folding or packing large, complex pieces of material, so we researched automated manufacturing for tent and sleeping bags. While we gained valuable insights from the analogous domain research, it made us realize that there is no automated process that closely matches parachute packing. We would have to see the process for ourselves to gain a better understanding of it.

Primary Research
Next, we conducted primary research through a contextual inquiry at Fort Gregg-Adams. A contextual inquiry is a great way to empathize with the user you are designing for—you go into their environment and watch them in action.
We spent 2 days at Fort Gregg-Adams, including touring the base and ADFSD facility, observing the riggers working, and conducting semi-structured interviews. We used the AEIOU method, looking at Activities, Environment, Interactions, Objects, and the User. This process can involve asking questions, taking notes, and silently observing how the user does their task and how they interact with their environment.
We used the AEIOU method, looking at Activities, Environment, Interactions, Objects, and the User. This process can involve asking questions, taking notes, and silently observing how the user does their task and how they interact with their environment.
Our research produced a wealth of findings that we still had to make sense of.

DEFINE
Finding the Problem Behind the Problem
Affinity Mapping
We took all of our findings and sorted them into groups based on similarities. From there, we could find common patterns and extract insights.










Some key findings were that there was a high incentive for efficiency—riggers can go home once they successfully complete 15 parachute packs. As a result, balancing efficiency with quality, especially during times of high stress like "push weeks", was very hard. The physically taxing, repetitive work often results in strain and injury. Finally, the work is hard, so boosting morale is important. They play loud music, compete with each other, and have a strong sense of camaraderie to get through the day.
Insights
These took a few rounds of iteration before we solidified them. We had to summarize key findings, while also telling the client something they didn’t already know. In short, “...So What?”
Rigger reliance on inspectors (1:4 inspectors:rigger ratio) is a bottleneck for packing efficiency
Not relying completely on inspectors to move to the next step can increase rigger efficiency while maintaining safety standards.
The one-size-fits-all approach to the packing process disregards individual ergonomics, resulting in strain and injury
A shift towards a more adaptable process can foster a healthier work environment and boost productivity
Limited variability and collaboration makes work monotonous, impacting rigger morale and job satisfaction
We can increase rigger engagement and satisfaction by addressing the monotonous nature of parachute packing
Small, inefficient tasks, add up throughout the day, wasting riggers’ time and reducing manpower
By optimizing parts of the parachute packing process, we can free up manpower and improve efficiency
Guiding Principles
We reworked our insights into actionable questions that helped guide us through the rest of our journey.
How might we make the process less physically demanding and reduce repetitive motions?
How might we collect and analyze performance data to optimize packing techniques?
How might we develop modular packing techniques that allow for faster and/or scalable rigging?
How might we facilitate team collaboration without losing accountability?
DEFINE
Finding the Problem Behind the Problem
Affinity Mapping
We took all of our findings and sorted them into groups based on similarities. From there, we could find common patterns and extract insights.










Some key findings were that there was a high incentive for efficiency—riggers can go home once they successfully complete 15 parachute packs. As a result, balancing efficiency with quality, especially during times of high stress like "push weeks", was very hard. The physically taxing, repetitive work often results in strain and injury. Finally, the work is hard, so boosting morale is important. They play loud music, compete with each other, and have a strong sense of camaraderie to get through the day.
Insights
These took a few rounds of iteration before we solidified them. We had to summarize key findings, while also telling the client something they didn’t already know. In short, “...So What?”
Rigger reliance on inspectors (1:4 inspectors:rigger ratio) is a bottleneck for packing efficiency
Not relying completely on inspectors to move to the next step can increase rigger efficiency while maintaining safety standards.
The one-size-fits-all approach to the packing process disregards individual ergonomics, resulting in strain and injury
A shift towards a more adaptable process can foster a healthier work environment and boost productivity
Limited variability and collaboration makes work monotonous, impacting rigger morale and job satisfaction
We can increase rigger engagement and satisfaction by addressing the monotonous nature of parachute packing
Small, inefficient tasks, add up throughout the day, wasting riggers’ time and reducing manpower
By optimizing parts of the parachute packing process, we can free up manpower and improve efficiency
Guiding Principles
We reworked our insights into actionable questions that helped guide us through the rest of our journey.
How might we make the process less physically demanding and reduce repetitive motions?
How might we collect and analyze performance data to optimize packing techniques?
How might we develop modular packing techniques that allow for faster and/or scalable rigging?
How might we facilitate team collaboration without losing accountability?
IDEATE
Exploring Possible Solutions

Since we had principles to guide us, we could begin to think of potential solutions. We started with a modified version of “Crazy 8s”. Normally, you would have 8 minutes to draw 8 potential solutions to a problem statement. However, we did crazy “15” since we gave everyone 15 minutes per principle. We generated 200 ideas, give or take a few.
Refining
We couldn’t show the client 200 ideas, so we took out duplicates, combined similar solutions, and sorted them into broader categories. Four main categories developed: ergonomics & physical assistance, workflow automation & tooling, in-process monitoring & data collection, and organizational changes. Now, we could sort the ideas based on how much they satisfied insights and see which categories offered the biggest gains.


Ergonomics & Physical Assistance

Work flow Automation & Tooling

In-process Monitoring & Data Collection

Organizational changes

Combined, our four categories addressed each of the four problem areas.
Concept Sketches
Left with 4 solution categories, we wanted to visualize them in a way that could start a dialogue with the client. We opted for a sort of abridged storyboard—basically, concept sketches with added backstory. If we were to show them highly-polished, refined solutions, they naturally would be less inclined to comment negatively. This low-stakes depiction of our ideas allows the client to share their honest thoughts.





IDEATE
Exploring Possible Solutions

Since we had principles to guide us, we could begin to think of potential solutions. We started with a modified version of “Crazy 8s”. Normally, you would have 8 minutes to draw 8 potential solutions to a problem statement. However, we did crazy “15” since we gave everyone 15 minutes per principle. We generated 200 ideas, give or take a few.
Refining
We couldn’t show the client 200 ideas, so we took out duplicates, combined similar solutions, and sorted them into broader categories. Four main categories developed: ergonomics & physical assistance, workflow automation & tooling, in-process monitoring & data collection, and organizational changes. Now, we could sort the ideas based on how much they satisfied insights and see which categories offered the biggest gains.


Ergonomics & Physical Assistance

Work flow Automation & Tooling

In-process Monitoring & Data Collection

Organizational changes

Combined, our four categories addressed each of the four problem areas.
Concept Sketches
Left with 4 solution categories, we wanted to visualize them in a way that could start a dialogue with the client. We opted for a sort of abridged storyboard—basically, concept sketches with added backstory. If we were to show them highly-polished, refined solutions, they naturally would be less inclined to comment negatively. This low-stakes depiction of our ideas allows the client to share their honest thoughts.





Prototype
We are working on this stage! See our Design Page for more details
Prototype
We are working on this stage! See our Design Page for more details